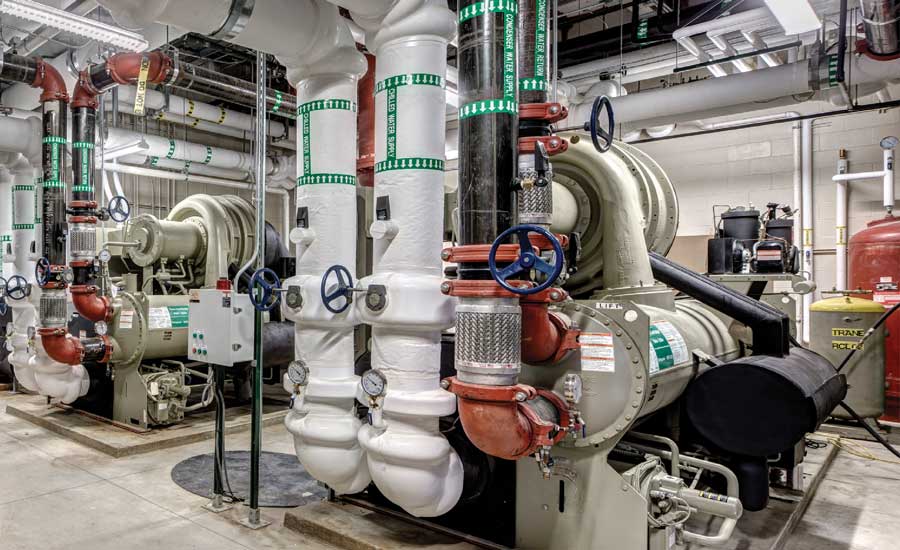
Despite your business size or your process of production downtime can be interruptive causing large expenses and other issues while trying to reach the demands of the customers. Industrial chiller maintenance is important in mitigating downtime risks, extending equipment lifetime, and giving you peace of mind that you are doing everything possible to keep the production process operations and reduce downtime.
The functions of a chiller maintenance checklist are:
- Give you daily basics for keeping things operating smoothly.
- Give you information on the best chiller maintenance practices.
- Give you advice on what to pay attention to while checking your machine’s refrigeration circuit.
- Informs you to have an educative conversation while choosing your planned preventative maintenance contractor.
You are supposed to be F-Gas certified to operate temperature-controlled equipment. You should ensure that the operator is fully qualified. However, there are some basic things that you can do daily to keep things operational.
The basics
Just like a car, making regular daily inspections on industrial chillers can help in preventing breakdowns. Making regular checks that take less than two minutes daily could make a big difference to your operations and help you prevent rather than fix.
Ensure that you check for abnormal vibrations or sounds. You can also conduct visual checks such as looking for debris in the areas around the chiller as well as loose components like thermal insulation. Check for excessive condensation and fluid leaks.
If the chiller is showing fault codes you can look for an expert and avoid settling for a stop-gap measure to keep operations going. If you do so you might void your warranty if conducted without caution and will cause heavy damage to your machine as well.
Do not allocate these checks to a single individual as such issues discussed above can quickly escalate into more serious faults. Ensure that you print a daily log so that staff can be able to ensure that the equipment has been checked daily. Train employees on running basic checks if they have not been done.
Comprehensive look
You will need to find time to conduct a thorough inspection of your machinery may be weekly or monthly without a fail. By planning this sooner you can be able to meet production needs. Preventable downtime is worse than planned downtime.
You will be obliged to remove the side panels of your equipment to commence checks. You should also check for debris inside the chiller in addition to your daily routine.
It is vital to disconnect the equipment from the electrical supply during an inspection.
When the unit is safe you can check the fastenings and fixings on the unit making sure that they are tight enough. You should also check for leakages and check all pipe works to make sure that no liquid is leaking or seeping from the machinery. If you suspect anything you should not hesitate to call an expert.
Make sure that you safeguard against the potential of condensation or leakages on your equipment by checking the enclosures and boxes on the equipment are sound. Check locks, hinges, and screws are properly placed.
Refrigeration circuit
This should be conducted by certified engineers. Before making any maintenance activities on the refrigeration circuit. The engineer should have a look at the logs you have been keeping since the last check. After checking the surroundings of the unit like ambient temperature the other three main parts of the circuit should be inspected.
Chiller compressor
This component operates as a pump for the unit’s refrigerant by using pressure differences to move the liquid around the system. There are important things to discuss with your engineer or you can check them yourself:
- Sanction pressure and temperature
- Discharge pressure and temperature
- Pressure and oil level
- Current levels and voltage.
Chiller evaporator
The next part to inspect is the evaporator whose major function is taking the absorbed heat from your plant. Depending on the chiller type either water or air-cooled these checks will differ slightly. The major points to check are:
- Air inlet or fluid pressure and temperature
- Air outlet or Fluid pressure and temperature
- Refrigeration outlet and inlet temperature
- Condition of insulation.
Chiller condenser
The last component is the condenser. Its main function is removing the heat taken to the refrigerant by the compressor. There are two types of condensers water-cooled and air-cooled which will slightly change your checks:
- Exhaust temperature and air intake
- Refrigeration outlet and inlet temperature
- Noise, fan motor currents, and vibration.
- Condition of the condenser coil,
Dosing of Chiller glycol
There are other things that you should put into consideration. You should look at your chiller’s glycol dosage. Glycol is antifreeze and prevents the fluids inside the chiller from freezing since it handles temperatures below zero. If poorly managed the water in your chiller will freeze damaging the pipework and causing production downtime while resolving the issue.
Do not use generic glycol the glycol in your system needs to be inhibited. This means that it has been specifically made to not corrode your pipework.
Chiller water treatment
Do not ignore the water quality when checking your chiller water system. The quality of water is important and failing to manage it will cause corrosion of pipework which will lead to failure of equipment. It is a legal requirement to check water quality and most service providers won’t action low results they will just inform you of them.
Leak testing
The leak test is the most important maintenance action of any refrigeration circuit inspection. You first need to allow the equipment being used by your engineer to be used on your system. A leak test makes sure that the circuit is sealed hermetically.
All refrigerants have a greenhouse effect potential hence if there is any difference between the levels of the refrigerant and the expected levels the disparity source needs to be detected verified and fixed before recharging the refrigerant.
In summary, coming up with an action plan will rely on the results of your routine checks or refrigeration circuit checks. This could also involve a water treatment program or simply repairing your machinery. You can consult a contractor to conduct exhaustive planned preventative maintenance programs for smooth production and peace of mind.
