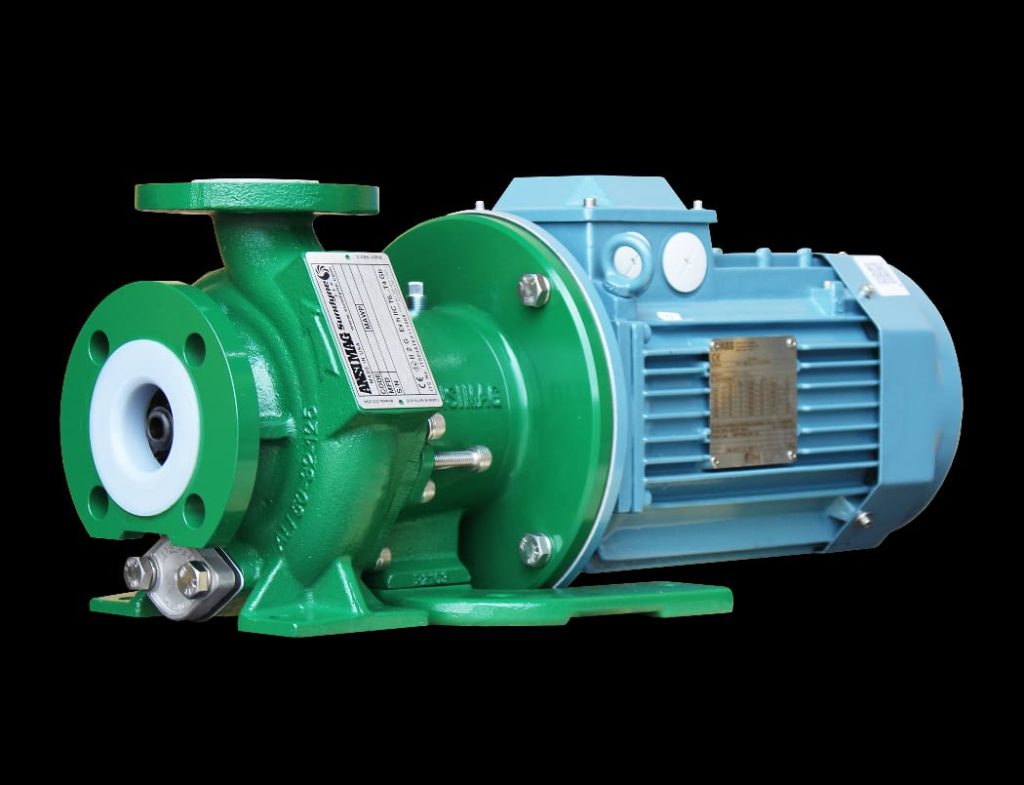
Introduction
Chemical transfer pumps are essential equipment in industries that deal with the transfer of various chemicals, solvents, and corrosive liquids. These specialized pumps are designed to safely and efficiently move fluids from one location to another, ensuring the integrity of industrial processes and minimizing the risk of accidents orenvironmental contamination. In this article, we will explore the importance of chemical transfer pumps, their working principles, key features, and the diverse applications they serve in different industries.
The Significance of Chemical Transfer Pumps
Chemical transfer pumps play a crucial role in industries such as manufacturing, agriculture, pharmaceuticals, water treatment, and many others. They facilitate the movement of fluids throughout different stages of production, ensuring a continuous flow and precise control over the transfer process. These pumps are designed to handle aggressive chemicals, corrosive substances, and hazardous liquids, thereby protecting the equipment, ensuring worker safety, and preventing environmental damage.
Working Principles of Chemical Transfer Pumps
Positive Displacement Pumps: Positive displacement pumps trap and transfer fluid by creating a series of chambers or cavities. These pumps include reciprocating pumps (such as piston pumps and diaphragm pumps) and rotary pumps (such as gear pumps and screw pumps). Positive displacement pumps are ideal for applications requiring precise flow control, high pressure, and the ability to handle fluids with varying viscosities.
Centrifugal Pumps: Centrifugal pumps use centrifugal force to move fluids. They work by rotating an impeller, which creates a vacuum that draws in the fluid and then propels it outward. Centrifugal pumps are commonly used for transferring large volumes of low-viscosity fluids, making them suitable for applications where high flow rates are required.
Air-Operated Double Diaphragm (AODD) Pumps: AODD pumps use compressed air to alternate the movement of diaphragms, creating suction and discharge pressure. These pumps are self-priming, can handle solids and abrasive fluids, and are known for their reliability and versatility.
Key Features and Considerations for Chemical Transfer Pumps
Chemical Compatibility: It is crucial to select a pump that is compatible with the specific chemicals being transferred. Consider factors such as chemical composition, concentration, temperature, and potential reactivity with pump materials. Choosing the right pump material, such as corrosion-resistant plastics, stainless steel, or specialty alloys, ensures long-lasting performance and prevents chemical reactions.
Seal Options: Chemical transfer pumps should have effective sealing mechanisms to prevent leakage and ensure the safety of personnel and the environment. Options include mechanical seals, packing seals, and seal-less designs like magnetic drive pumps, which eliminate the risk of leakage.
Flow Rate and Pressure: Determine the required flow rate and pressure for your application to select a pump that can meet these specifications. Consider factors such as the distance of fluid transfer, elevation changes, and any restrictions in the piping system.
Safety Features: Chemical transfer pumps should be equipped with safety features to protect against potential hazards. These features may include leak detection systems, pressure relief valves, explosion-proof ratings, and compliance with industry-specific safety standards.
Maintenance and Reliability: Consider the ease of maintenance, availability of spare parts, and the reputation of the pump manufacturer. Regular maintenance and proper upkeep ensure the longevity and reliability of the pump, reducing downtime and optimizing operational efficiency.
Applications of Chemical Transfer Pumps:
Chemical transfer pumps find applications in various industries, including:
Chemical Manufacturing: Chemical transfer pumps are extensively used in the production, processing, and storage of chemicals, ensuring the safe and controlled movement of raw materials, intermediates, and finished products.
Agriculture: These pumps are employed in agricultural settings for tasks such as transferring fertilizers, pesticides, and irrigation fluids, supporting efficient crop production.
Pharmaceuticals: Chemical transfer pumps are vital in pharmaceutical manufacturing processes, enabling the precise dosing, mixing, and transfer of active pharmaceutical ingredients (APIs) and other chemicals used in drug production.
Water Treatment: Chemical transfer pumps play a crucial role in water treatment facilities by transferring chemicals for disinfection, pH adjustment, coagulation, and flocculation, ensuring clean and safe drinking water.
Mining and Oil Industries: These pumps are used for handling corrosive chemicals, acids, and solvents in mining operations and the extraction, refining, and transportation of oil and gas.
Conclusion
Chemical transfer pumps are indispensable in industries that require the safe and efficient handling of corrosive, abrasive, and hazardous fluids. By carefully considering factors such as chemical compatibility, flow requirements, safety features, and maintenance needs, industries can select the right chemical transfer pump for their specific applications. Investing in reliable and high-quality pumps ensures the smooth operation of industrial processes, protects workers and the environment, and contributes to overall productivity and efficiency.

Hello! Would you mind if I share your blog with my twitter
group? There’s a lot of folks that I think would really appreciate your content.
Please let me know. Thank you
Have a look at my page – Nordvpn coupons inspiresensation
350fairfax nordvpn
I blog quite often and I truly appreciate your content.
The article has truly peaked my interest. I am going to bookmark your blog and keep
checking for new details about once per week. I subscribed to your RSS feed too.
whoah this weblog is excellent i love reading your articles.
Stay up the good work! You recognize, a lot of people
are looking around for this information, you could help them
greatly.
Take a look at my web blog: eharmony Special coupon code 2025
I must thank you for the efforts you’ve put in penning this blog.
I’m hoping to check out the same high-grade content by you in the future as well.
In truth, your creative writing abilities has motivated me to get my own, personal blog now 😉
Check out my homepage: vpn